New 'Vibrant Pack Energy Harvesters' to Harness Big Bridge Vibrations

This story by Craig McManamon first appeared in the Heriot-Watt University (Edinburgh, Scotland) newsroom and has been tailored for Georgia Tech audiences.
Traffic and wind regularly cause low frequency vibrations to ripple through bridge building materials such as steel and concrete. This energy would normally travel away from its source before dissipating — but academics at Heriot-Watt University in Edinburgh alongside colleagues from Georgia State University and Georgia Tech in the US have recognized an opportunity. They intend to capture and recycle this untapped source by using the principles of physics.
They have received £340,000 (about $463,000) from the Engineering and Physical Sciences Research Council (EPSRC), part of UK Research and Innovation, and $443,000 from the National Science Foundation (NSF) to research and develop a revolutionary vibro-impact energy harvesting device.
Daniil Yurchenko, Ph.D., from Heriot-Watt University, has created a prototype called a ‘vibrant pack energy harvester’ that can be fitted at multiple locations on a bridge.
These autonomous devices, measuring around 5 – 10cm in length, do not require wiring to an electrical power source and are relatively cheap to manufacture. They work by holding a small ball housed within a tube that rolls back and forth as the device absorbs low frequency vibrations. As the ball moves, it impacts on non-conductive materials, known as dielectric membranes, located at either end of the tube. When the membrane is stretched, a brief electrical charge is applied but once it returns to its undeformed state, the generated excessive electrical charge can be harvested.
This electrical energy is stored in a battery and used to power a sensor capable of monitoring the structural integrity of a bridge. Engineers can then record multiple measurements, such as vibrations, traffic load, wind and temperature, all at the same time but without the need for specialist infrastructure to be installed at significant cost.
Yurchenko, from the School of Engineering and Physical Sciences at Heriot-Watt University, explains that while dielectric elastomer technology has been tried in wave energy, nothing has been done on this centimetre scale before.
“What we are doing is creating a more efficient and cost-effective solution by harvesting energy that would otherwise be lost,” he said.
“It’s something that has never been done before in this way.
“It’s a technology that can be used on any bridge anywhere in the world. There are plenty of places where these devices can be fitted to a bridge structure such as on cables, on the pillars, other side of the bridge deck, there really aren’t any limits.
“The biggest problem in energy harvesting is that the absolute amount of energy produced by a typical device is very small due to the low available level of vibrations. In fact, for the past 100 years scientists have been fighting adverse vibrations to ensure that bridges are safe. So, through this work we will try to optimise the performance of our vibro impact energy harvesting device tuning it to the bridge application.”
The team is working alongside Wenzel Consult, an independent company that specialises in bridge sensor technology in Austria and Turkey.
As the project advances, the scientists say they intend to carry our real-life testing of their prototype on a 32-meter long highway bridge in northern Austria.
The multidisciplinary project, entitled, Stochastic Nonsmooth Analysis For Energy Harvesting, is due to complete in 2024.
Rachel Kuske, professor and chair of the School of Mathematics at Georgia Tech, said: “While the device has nonlinear behaviour, which is beneficial in generating more energy than is used to power the device, the same nonlinearity can result in a range of complex responses to the vibrations.
“We will use dynamical analyses to predict the different types of responses, as well as to select design choices for responses that optimise energy output. As the bridge vibrations are also inherently noisy, the analysis will also identify how to leverage noise sources that are beneficial and mitigate effects from detrimental noise sources.”
Professor Igor Belykh, co-investigator from Georgia State University, adds: “This project seeks to provide guidelines for designing power supplies that can harvest energy from bridge oscillations. These energy harvesters can be used in bridge damage sensors thereby minimising sensor maintenance/battery replacement and decreasing the associated risks to service personnel on high suspension bridges. Moreover, this project is synergistically connected to another project supported by NSF grant (2019-2022) ‘Modern approaches to modelling and predicting bridge instabilities’ that will inform the design of energy harvesters by offering a dynamical characterisation of bridge oscillations and external perturbations to be harvested.”
The scientists say that in the future the same technology could be adapted and used to harvest energy from other vibrating man-made structures and machines.
Related news coverage: Edinburgh Evening News, Scottish Construction Now, FutureScot, The Herald Scotland, Digit
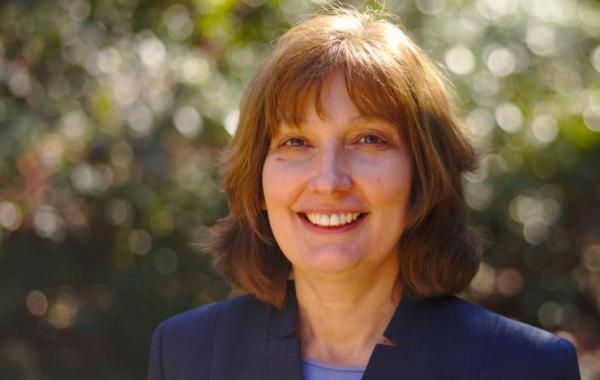
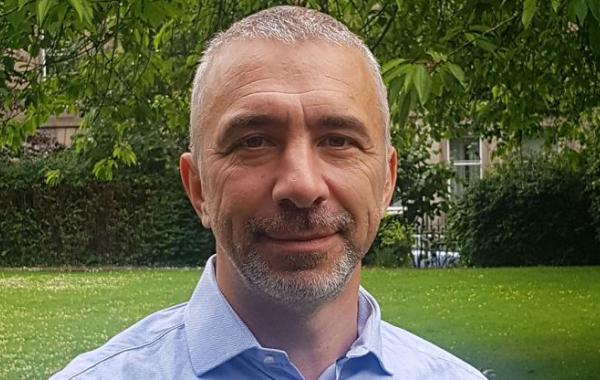
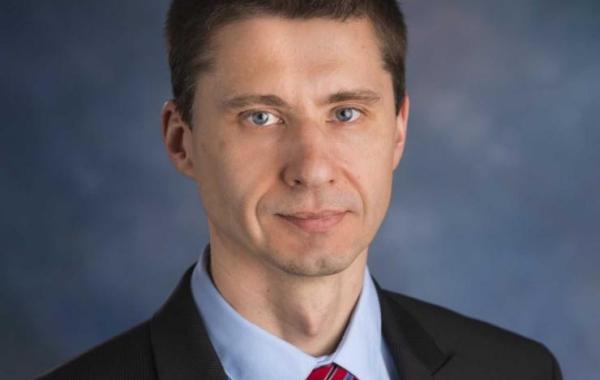